The linear supply chain — the traditional supply chain model that maps a straight product path from raw materials, to production, to distribution to waste — is now going the way of the video store.
When was the last time you drove to your local Blockbuster to pick up a film for date night? Or family movie night? Or just ‘you’ night?
Linear supply chains have been the norm for centuries now — but society is waking up to the flaws of the linear economy. Which means companies are looking for a new way to deliver their products and services that doesn’t rely on unsustainable business practices.
In this blog, we’re going to take a closer look into this change, exploring:
- The past and present of linear supply chains
- The flaws of the linear economy
- The next step in supply chain evolution
A brief history of the linear supply chain
Ready for a whistle-stop tour?
Early examples of linear supply chains included ancient trade routes like the Silk Road in Central Asia and the Spice Route over the Indian Ocean.
They served a key purpose at the time, taking raw materials like silk, spices, ivory, wool, cotton and precious metals from their point of origin to their end consumer; the basis for all supply chains to come.
Limited by their time, most supply chains were localized. Until the next great evolution. Upgrades in shipping design and the opening of canals like the Suez and Panama revolutionized transportation. Goods could now be supplied internationally.
Fast forward a few decades, and supply chains were further extended by the growing availability of planes, trains and automobiles. This opened up trading massively, and allowed mass manufacturers to open factories in more financially desirable geographical locations and transport goods to customers at faster speeds.
With the technological advancements made in the industrial revolution, ‘Fordist’ linear production lines became the model to copy. Goods could be produced in greater quantities at lightning-quick speeds.
The next step? Communications. The telephone, internet and digital communications allowed companies to network and contract different parts of the supply chain, decentralizing production. This was especially prevalent in the emerging electronics industry.
Now, digitization and data can give companies even greater insight into every aspect of how products are produced and moved from factories to consumers, putting the focus back on the customer.
The modern problem with linear supply chains
The world has a way of illuminating flaws in design. Although linear supply chains have long faced criticism for their wasteful and polluting nature, it was the COVID-19 pandemic that put the words “supply chain” on everyone’s lips — and made people really sit up and take notice of the inherent flaws within the linear model.
Ecological issues
According to Nielson, 66% of global customers say they’re willing to pay more for sustainable products. That’s something the linear economy tends to ignore.
Linear supply chains operate on a “take-make-waste” model. Raw materials are sourced, turned into products and parts, delivered to the consumer, then discarded at the end of their lifecycle. It’s inherently unsustainable.
The extraction of raw materials requires a huge amount of energy consumption, which creates high emissions of CO2 and displaces natural ecosystems. Metal mining has negative environmental impacts such as deforestation, erosion, contamination of soil, streams and air quality and negatively affects biodiversity by destroying habitat.
The making of parts and products is another big contributor to climate change. Plastic production alone added more than 850 million metric tons of greenhouse gasses to the atmosphere in 2019.
Most waste ends up in landfills. The EPA estimates that 103.9 million metric tons of CO2 is produced by landfills in the U.S. alone. And that isn’t counting the emissions caused by transportation to landfills.
Economic issues
The linear economy also impacts the general supply of materials, causing a huge amount of uncertainty.
Raw material prices have fluctuated dramatically over the past two decades, preventing companies without sophisticated AI and predictive analysis capabilities from accurately forecasting costs of production.
And when forecasting is so hit-or-miss, businesses everywhere are unprepared for external disruptions — meaning they suffer when supply drops unexpectedly, making them far less competitive.
The global linear economy also encourages interdependence of certain raw materials. For example, a lot of material production relies on water and fuel — so when one of those two raw materials dwindles, other material production is affected.
It’s also accelerated the decline in product lifecycles. Increased customer demand has led linear supply chains to use cheaper modes of production, which leads to decreased product durability. That, in turn, means consumers are using and discarding products faster, which then leads to a need for replacements. Rinse and repeat.
Operational issues
When parts of the linear supply chain are networked and disconnected, the lack of visibility and transparency becomes (ironically) all the more visible.
If one aspect of the supply chain fails, it’s felt by the whole supply chain through a domino effect. And because data isn’t shared downstream, other affected teams won’t be prepared or informed enough to play catch up, causing even more delays.
Reliance on raw materials increases costs, while inefficient journey planning increases costly truck runs and emissions.
Considering millions of dollars in recoverable materials is currently being lost to landfill, there’s a big opportunity at hand here.
Reverse logistics: Part of the solution, but not all of it
Reverse logistics is the process of reclaiming products and parts from end customers, moving them back to the manufacturer.
Industries have been incorporating reverse logistics into their supply chains for decades. And it does have a crucial role to play in the circular economy — because that process of moving items back to the manufacturer is essential to the refurbishment and repurposing cycle.
However, traditional reverse logistics often isn’t well thought out enough to result in true supply chain sustainability.
Reverse logistics is often entirely separate from the primary chain. Because of this:
- Product data is scarce, so teams are unable to predict the cause of faults or the end-of-life estimation
- Field agents are ill-equipped to deal with unique product cases, so treat each fix the same (usually ship back to the mothership warehouse, instead of looking for more efficient solutions)
- Lack of data visibility means the process of refurbishment and reuse is slow and inaccurate, meaning the most sustainable option is often lost or the product still ends up as waste
- Unnecessary transport, staff and storage costs are incurred due to inefficient recovery planning
Instead of guaranteeing circularity, ill-designed reverse logistics processes instead move the model from “build, ship, waste”, to “build, ship, recover, waste”.
To become truly circular, the reverse logistics process needs to be considered an essential part of the supply chain process — one where reclamation, refurbishment, reuse and recycling are purposeful objectives rather than incidental wins.
The better way forward: Circular supply chains
It’s time for linear supply chains to move over and make way for its successor: The circular supply chain.
The circular supply chain unites every aspect of production into a self-sustaining loop — one that continually services, refurbishes, reuses and recycles products and parts. It’s a model built for maximum efficiency and sustainability.
Circular supply chains:
- Unite historical and current data to determine the next best step for every individual part and product
- Allow for better recovery planning with real-time insight into product life cycles
- Reduce costs and maximize product value by keeping materials in circulation
- Improve environmental sustainability by keeping materials out of landfill
- Reduce the economic risks from volatile raw material supply and protect you against external disruptions like price fluctuations
- Help you meet new and growing regulation standards set by countries to encourage circularity, such as the European Green Deal and the EU Packaging directive
But embracing circularity is easier said than done.
That’s where we can help.
—————————
OnProcess provides technology and services to power the world’s circular service supply chains. With its proprietary platform, OnProcess Agora™, it allows data from otherwise siloed systems to be brought together to provide deep service insight and to drive intelligent and integrated circular service supply chain processes.
Want to learn more? Get in touch with us today for a free consultation and demo.
RELATED CONTENT
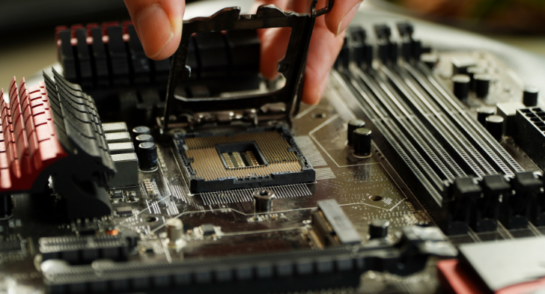

Infographic: Is anyone using AI and Machine Learning in the Service Supply Chain?

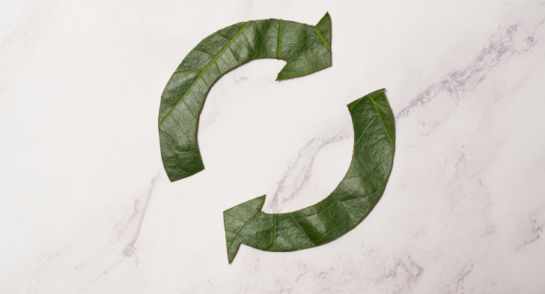
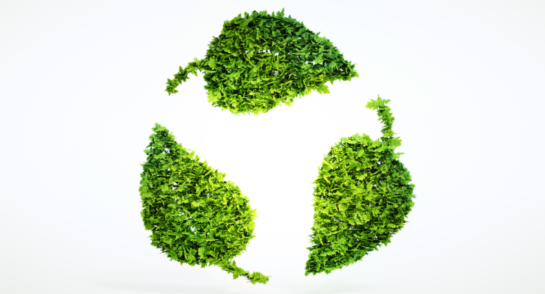
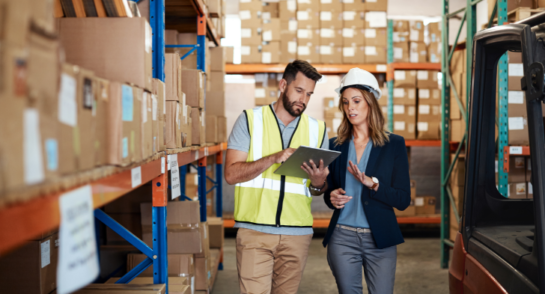
Sign up for updates
Get the latest updates on our new services and fresh content — straight to your inbox.