The reclamation of goods from a typical final destination back to the supplier or manufacturer was coined “reverse logistics” in the 1990s. But in recent years, as global focus shifts to the looming climate crisis and large-scale supply chain disruptions, it is being linked with another hot topic: Sustainability.
Businesses around the world are beefing up their sustainability ambitions, with 71% of companies saying sustainability is already integrated into their company strategy. The Science Based Target Initiative (SBTi), which supports businesses in setting ambitious emission reduction targets that are in line with the latest climate science, reports exponential growth in commitments, covering 2,253 companies with a joint market capitalization of $38 trillion. Alongside this, the reverse logistics market is expected to reach an eye-popping $812.6 billion by 2027.
Organizations looking to make sustainability an integral part of their process (and turn it into a profitable practice along the way) have turned to reverse logistics to make quick wins.
However, reverse logistics alone doesn’t result in the most sustainable outcome. The full potential of reverse logistics only unfolds when it’s done right — and, more often than not, that’s not the case.
So, what is the truth behind the relationship between reverse logistics and sustainability? And how can this be leveraged for maximum impact?
Reverse logistics and sustainability
Reverse logistics (the process of reclaiming parts and products) can undeniably assist businesses in making commercial and environmental sustainability gains — especially when done with the intent of refurbishment or reuse.
53.6 million metric tons of electronic waste was generated in 2019 alone, and this number is set to grow at around 2.5 tons per year. Experts estimate that the value of raw materials in landfills from this e-waste totals around $57 billion. Reverse logistics can help businesses capture this value in the most straightforward way: by diverting valuable finite materials from landfill (from which point businesses can determine the best way to re-introduce them to the market, whether through refurbishment, reuse or resale).
This process typically happens separately to the rest of the supply chain, and can help businesses:
- Reduce the environmental impact of e-waste and comply with environmental legislation
- Save on the costs of losing retrievable and reusable materials
However, viewed in isolation, reverse logistics is not enough to guarantee consistent sustainability.
Incidental sustainability: Why reverse logistics alone is not enough
While reverse logistics may result in some sustainability gains, they tend to be incidental to the process.
Reverse logistics naturally supports more sustainable operations; but the act of reclaiming products at end of life alone doesn’t necessarily result in big environmental wins. Other factors, such as what’s done with the products and freight emissions, also need to be taken into account.
Part of the problem is that the reverse logistics process tends to be carried out in isolation, meaning there’s little to no visibility over data generated throughout the process — and that’s a problem, because that data is essential to optimize and streamline processes across the supply chain.
This lack of data visibility leads to inefficient planning and decision making without consideration of all factors — which means companies don’t get the most value out of parts or find the most ecologically sound ways of conducting their business.
For example, let’s say a laptop is coming to the end of its lifecycle. A company using reverse logistics might:
- Identify this and send a field agent to collect the parts
- Transport the parts back to the main warehouse
- Decide from there whether to reuse, refurbish or resell the parts
However, our customer isn’t local, and lives considerably far away from the warehouse. What’s more, the laptop is salvageable with very few repairs needed.
While it avoids landfill, the cost (both financially and environmentally) of lengthy transport, storage, the lost value of a functional product and the cost of staff for what could have been a simple fix is unnecessary.
Without additional information, businesses will only land on the most efficient outcome some of the time, as:
- Siloed data and departments lead to a lack of visibility and impact decision making
- Lack of real-time tracking means optimized recovery trajectories for individual cases are rarely possible
- Transport emissions and material savings are not always considered as variables to optimize for
- Field engineers are unaware of other courses of action, so cannot adopt the most efficient response to individual cases in real time
- Lack of insight means parts are sent on unnecessary journeys, detracting from overall cost-effectiveness and ultimately damaging the environment
However, our example company likely already had all the data they needed to take action and reach a more sustainable outcome — they just didn’t have the capability to extract it and pull useful insight from it.
A better way forward: Long-term sustainability and the circular economy
For long-term success — and sustainability — companies need to rethink how to organize and optimize their entire service supply chain operations. From planning, to delivery to recovery: companies need to unite their data to enable accurate and sustainable decisions.
When data is integrated across the product’s full life cycle, recovery becomes an integral part of the process with crucial bottom line impact rather than just an afterthought. This means it is baked into the entire process, contributing to making a more circular (and less linear) service supply chain.
Having full integration, and visibility, of your data — along with the predictive power of AI — means you can maximize the value of every decision, allowing you to:
- Accurately forecast product and service parts demand to avoid unnecessary parts storage and truck runs
- Learn from past and current data to optimize faster, more accurate delivery routes that result in lower emissions
- Use holistic and smart parts data, so you can select optimal recovery trajectories, brief your engineers on exactly what’s wrong with parts well in advance, and predict what will go wrong before service events occur
- Determine the most efficient next step for products sooner, at the point of collection, to avoid unnecessary transport
Let’s go back to our laptop example. Earlier, we showed how a lack of real-time data insights can lead to greater costs and emissions. With a few changes to your approach, you can not only reduce freight and handling costs, but integrate sustainability into every decision:
- The recovery team and field agents could have seen exactly what was wrong with the laptop and that it was a relatively small issue
- They could have searched for nearby locations for minimal repairs, without automatically transporting it back to the main warehouse
- They’d be instantly informed of the best way to deal with the product, from its status (repair, refurbish or replace) to the nearest point of call to take action at
If you want a service supply chain that effectively syncs planning, delivery and recovery to achieve true and cost-effective sustainability, you need the right technology to harness the power of data and AI.
————————
OnProcess provides technology and services to power the world’s circular service supply chains. With its proprietary platform, OnProcess Agora™, it allows data from otherwise siloed systems to be brought together to provide deep service insight and to drive intelligent and integrated circular service supply chain processes.
Want to learn more? Get in touch with us today for a free consultation and demo.
RELATED CONTENT
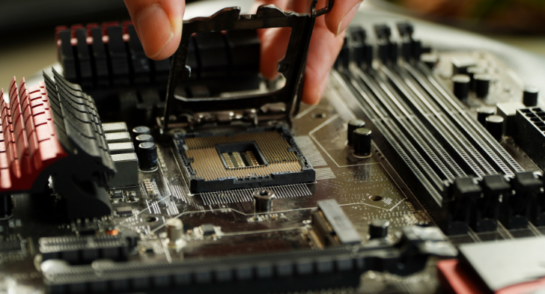

Infographic: Is anyone using AI and Machine Learning in the Service Supply Chain?
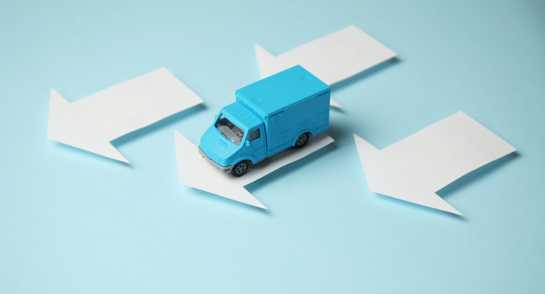
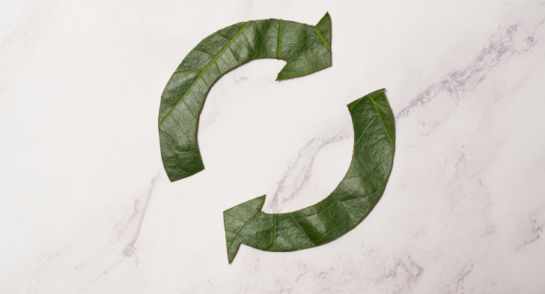
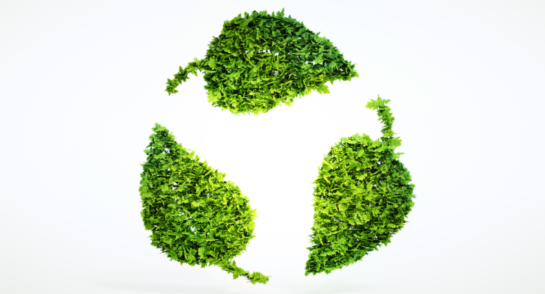
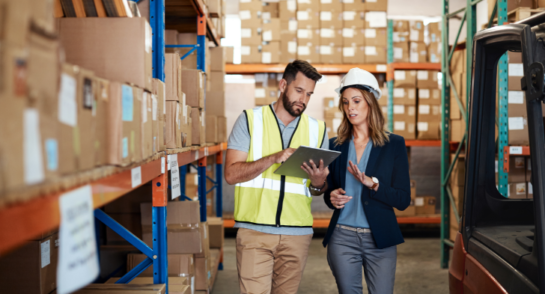
Sign up for updates
Get the latest updates on our new services and fresh content — straight to your inbox.